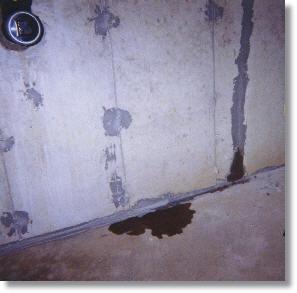
A vertical crack, weeping snap tie holes, and the floor joint repaired with Hydro-Epoxy Mortar.(3 parts fine sand, 1 part Portland cement, 1 part mixed Hydro-Seal 75. We used less than a gallon of Hydro-Seal 75 to repair all the cracks in this basement.
Hydro-Epoxy Mortar System
With the HYDRO-EPOXY MORTAR SYSTEM
deteriorated concrete surfaces can be patched and repaired. The result is
a waterproof, chemically resistant topping that will level and beautify
even the worst concrete substrates. This epoxy modified mortar consists
of cement, sand and Hydro-Seal 75 waterproofing.
In areas where pitted concrete has to be level to accept
NORTHERN SEAMLESS FLOORING & other types
of flooring, HYDRO-EPOXY MORTAR can be
applied as thin as required. Remember that most Seamless Flooring failures
are caused by inferior primers, excessive moisture, and lack of preparation.
With HYDRO-EPOXY MORTAR the worst deteriorated
substrate areas will be repaired and leveled with a waterproof, chemically
resistant, water-base epoxy mortar. Call Northern at 1 800 346 5543 for
chemical resistance information and detailed physical properties.
- I. INTRODUCTION By adding cement and dry sand to blended Hydro-Seal
75 components, a bonding mortar is created. This makes an excellent
crack filler, leveling and tuck pointing material for masonry joints.
Hydro-Seal 75 possesses tenacious bonding qualities as thin as required.
Hydro-Seal 75 is a solvent free, low modulus epoxy mortar binder designed
for mixing with suitable aggregate to provide a waterproof and wear
resistant slab topping for applications over Portland cement concrete
floor slabs.
- II. DESCRIPTION Hydro-Seal 75 Epoxy Mortar System consists of:
- A. Hydro-Seal 75
- B. CEMENT: No. 1 Portland (gray or white)
- C. SAND: No. 30 or No. 70 Sieve Dry Silica: Aggregate washed
kiln-dried graded and bagged silica sand containing a minimum of
98% silicon dioxide by weight aggregate shall be skip graded within
the following limits
Sieve Size |
Percent by weight
passing |
#4 |
100 |
#8 |
70 to 100 |
#16 |
33 to 75 |
#30 |
50 to 30 |
#50 |
5 to 20 |
#100 |
0 to 5 |
#200 |
0 to 3 |
- III. TYPICAL USES
- A. For substrate repair
- 1. Leveling
- 2. Resurfacing
- 3. Patching masonry
- B. For forming masonry
- C. As a coving system.
- IV. PHYSICAL ANALYSIS AND TECHNICAL
- A. Properties of cured binder when cured 7 days at 77° F and
tested at 77° F.
Tensile Strength |
ASTM D-638 |
2000 PSI |
Tensile Elongation |
ASTM D-638 |
25 % |
Compressive Yield Strength |
ASTM 695 |
2000PSI |
- B. Properties of Cured Mortar:3.1.1 by volume mix when cured
7 days at 77 degrees F and tested at 77 degrees F.
Tensile Strength |
ASTM C-190 |
1300 PSI |
Compressive Strength |
ASTM C-190 |
8000 PSI |
- C. CHEMICAL RESISTANCE TEST:HYDRO-SEAL 75 resurfacing mortar
will resist occasional splashing and spillage of practically most
chemicals without adverse effect, in most instances:
CHEMICAL |
EFFECT |
Detergent |
None |
Acetic Acid 3% |
Discolored |
Citric Acid 3% |
None |
Kerosene |
None |
Ammonium Hydroxide30% |
None |
Calcium Chloride 10% |
None |
Lactic Acid 3% |
None |
Mineral Spirits |
None |
Potassium Hydroxide 10% |
None |
Sodium Chloride 20% (Brine Solution) |
None |
Motor Oil Sol. 30 grade |
None |
Sugar Solution 30% |
None |
Steam (30 hrs) |
None |
Urine |
None |
Sodium Hydroxide 5% |
None |
Isopropyl Alcohol 100% |
None |
Textile Spirits 100% |
None |
Toluene 100% |
Discolored |
- V. APPLICATION
- A. Tools: Straight edge trowel, mortar mixer or wheel barrel
- B. Procedure:
- 1. Prepare Substrate:
- a) Conditions of surfaces shall be dry and free
of dirt, paint, grease, oil, rust and other contaminants.
- b) Surface shall be inspected and approved before
the work has begun.
- c) New concrete shall have been properly cured and
seasoned.
- d) Concrete surfaces shall be roughed by wire brushing,
sand blasting, chipping, or etching.
- e) All shrinkage shall have occurred.
- f) Defects shall be corrected. Open cracks by undercutting
or squaring off, rather than "V" cutting.
- 2. Mixing:
- 3. Apply to necessary areas with straight
edge trowel
- a) Patch all cracks and
voids, and cove all corners and joints.
- (1) Coving should extend
at least two inches out and up from floor
joints.
- (2) Areas around form-ties
in poured walls should be opened and patched.
- (3) Allow patching to
dry for two hours at 75°
F or until dry to the touch.
- C. For Thin hairline cracks
- 1. For a thickness Under 1/16"
a mixture of Hydro-Seal 75( mixed) and Portland
cement can be used without sand to feather edge
hairline cracks and bridge small voids. The amount
of cement added to the mixed Hydro-Seal 75 is determined
by the thickness of the crack.
- VI. CAUTION
- A. When skin contact occurs,
wash immediately with soap and water
- B. Do not
ingest.